燃料由来の金属成分やアルカリ成分、硫黄化合物によって、配管や設備機器は様々な腐食障害を引き起こされ、きちんとした温度管理や保全をしなければ、重大なトラブルに陥ってしまう可能性があります。
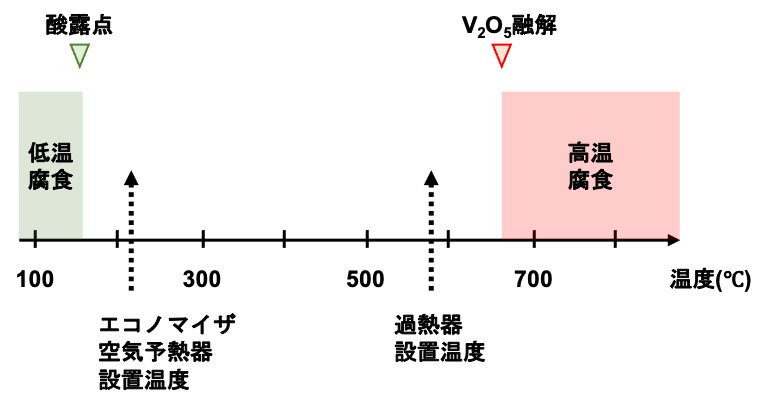
高温腐食とは
高温腐食とは、燃料中に含まれるバナジウム、ナトリウムなどの金属成分の酸化物を含んだ灰が、高温伝熱面(加熱器や再熱器)に付着、溶融し、母材金属の酸化被膜を溶解させる現象のことです。
通常、伝熱面の表面はその母材金属の酸化被膜で覆われて酸化の進行を防いでいますが、この上に灰が付着すると酸化被膜を溶かします。
バナジウム(V)は750〜1500℃で、五酸化バナジウム(V2O5)を生成しますが、V2O5の融点は675℃ですので、融解して腐食を引き起こします。
このような腐食をバナジウムアタックと呼んでいます。
また、ナトリウム(Na)やカリウム(K)のようなアルカリ金属は硫黄酸化物と結合して、硫酸ナトリウム(Na2SO4)などの硫黄化合物を生成します。
この硫酸化合物の存在下では、五酸化バナジウム(V2O5)の融点は550〜580℃に低下し、液体として存在しやすくなるため、腐食を促進させます。
高温腐食の対策としては次のようなことが挙げられます。
高温部の表面温度を下げるように、伝熱面の配置を考慮する(設計の工夫)
付着物をできるだけ落とすようにスートブローを適切に配置(設備の適正化)
添加剤の注入により、灰の融点を上げる(添加剤注入)
バナジウムやナトリウムの少ない原料を使用(原料の適正化)
低温腐食とは
低温腐食とは、燃料中の硫黄化合物が燃焼と燃焼後の反応により硫酸となり、その硫酸が凝縮して伝熱面を腐食させることです。
燃料を燃焼すると、燃料中の硫黄化合物は二酸化硫黄(SO2、亜硫酸ガスとも呼ぶ)となり、その中の1〜5%程度が三酸化硫黄(SO3、無水硫酸)に酸化すると言われています。
この三酸化硫黄と水蒸気が反応して、硫酸(H2SO4)を生成し、その硫酸が低温伝熱面に凝縮して腐食を引き起こしてしまいます。
また、このガス状の硫酸が凝縮し始める温度のことを、酸露点と呼びます。
燃料中の硫黄分、過剰空気量、水蒸気量、燃焼方法によっては酸露点は160℃まで上昇することがあり、低温腐食を引き起こす温度範囲を広げてしまいます。
低温腐食の対策としては、以下が挙げられます。
低温伝熱面が酸露点以下にならないように管理する(設計の工夫)
SO2→SO3への転換を低減するために、低空気比燃焼を行う(操業の適正化)
SO3の中和のためにドロマイト(CaMg(CO3)2)やアンモニアなどを燃焼室内に添加する(添加剤注入)
低硫黄分燃料を選択する(原料の適正化)
まとめ
今回は、高温腐食と低温腐食について解説しました。
温度のイメージ感を図にすると以下のようになります(縦軸は腐食速度にしたかったのですが、ちょっと難しかったです)。
もちろんここまできっちり温度で腐食域が区切られているわけではないので、注意してください。
以上、解説でした!